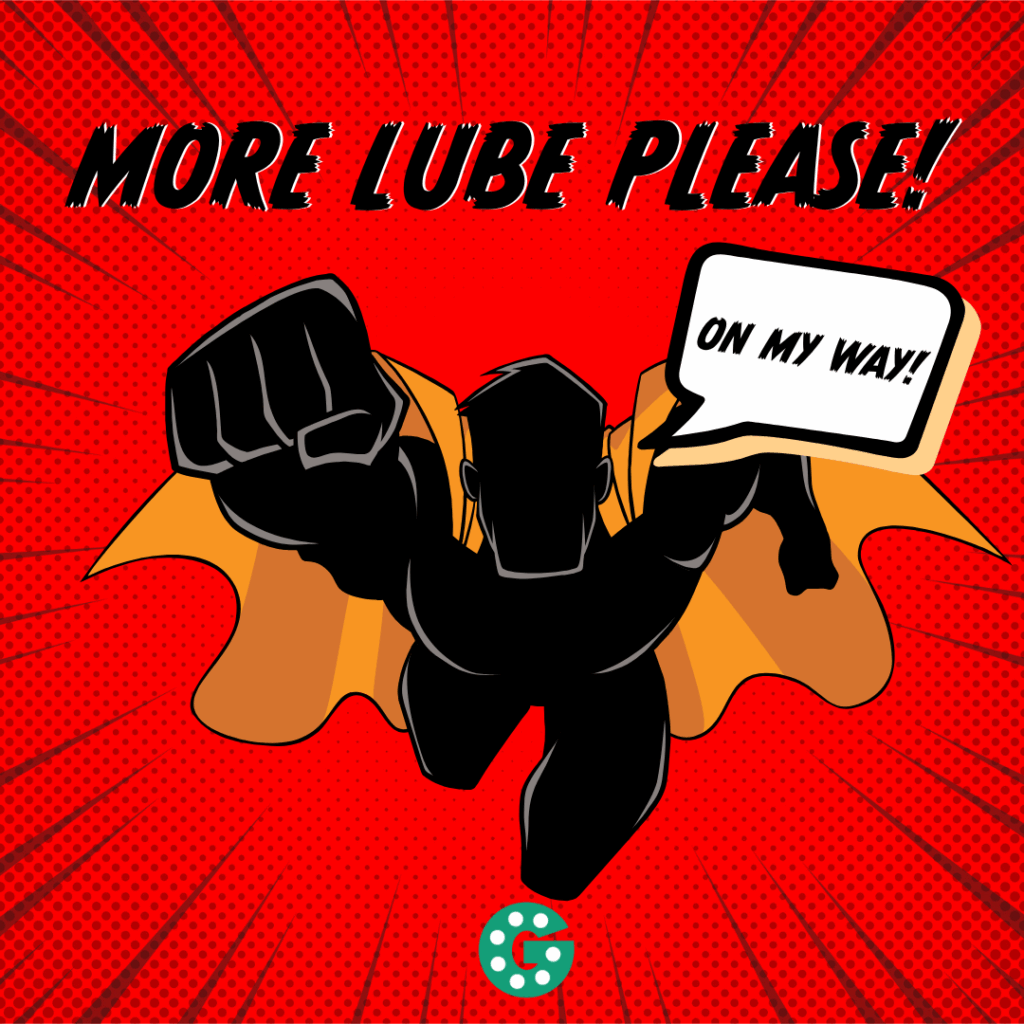
3 Hidden Causes of Downtime in Food Processing
Food Processing downtime is never convenient. Whether it delays a batch, causes a failed hygiene audit, or ruins a run of product, the effects ripple across the business. The worst part? Many of the issues that bring a production line to a halt start small and are entirely preventable.
Bearings are a common weak point. When mis-specified or installed without care, they can quietly cause major headaches. Most engineers will tell you that the bearing is the last place people look, but often the first place where problems start.
Here are three often-overlooked causes of downtime in food processing, plus one bonus issue that deserves more attention.
1. Bearings That Were Never Meant to Be There
Spec sheets matter more than price tags
Not all bearings are created equal. Using general-purpose components in food processing environments might save money upfront, but it’s a guaranteed path to bigger problems later. These environments are tough, humid, and aggressive. You need components that are built to survive constant cleaning and exposure.
What goes wrong with incorrect specs:
- Mild steel housings start to rust quickly.
- Non-food-safe grease contaminates the product zone.
- Basic seals fail under water pressure and heat.
Even if the bearing “fits”, that does not mean it’s suitable. The result? Worn inserts, leaking grease, and surprise shutdowns mid-shift.
2. Washdowns That Hide the Damage
Hygiene matters. But so does sealing. High-pressure washdowns can blast water, chemicals, and heat directly into vulnerable bearing zones. The result is usually not visible until a failure has already begun.
Signs of hidden damage:
- Grease becomes milky or leaks visibly
- Rust rings appear beneath housings
- Bearings fail days after a major clean.
This is often treated as “just one of those things”. In reality, it is a sign that the current bearing setup is not holding up to washdown cycles.
Simple ways to prevent failure:
- Use sealed units designed for harsh washdowns
- Train staff on correct spray angles and distances
- Inspect for pooling water or ingress after cleaning
- Re-lubricate immediately after the wash
3. Mounting Issues That Fly Under the Radar
Auto-lubrication systems like those from Perma help eliminate human error and ensure consistency, even on weekends and overnight shifts.
🛠 Check out: Perma lubrication systems
🔎 Also read: Food Line Washdowns: Hidden problems & Fixes.
How a sloppy install becomes a silent failure
Even a premium food-grade bearing will give up quickly if the mounting surface is poor. Flat, undrained surfaces trap moisture. If housings are not installed square or shaft alignment is off, the bearing wears unevenly. These problems rarely make noise. They just reduce lifespan one day at a time.
Watch out for:
- Bearings failing repeatedly in the same location
- Uneven wear on housings or inserts
- Grease loss or pressure at one side of the seal.
Good practice includes:
- Sloping mounts for proper drainage
- Raising housings above pooled water areas
- Checking shaft alignment during installation
- Using shims where necessary to maintain fit.
Don’t assume the part is the issue. Sometimes, it is the pad it’s sitting on.
Bonus Cause: Ignoring Re-Lubrication Schedules
The fastest way to wear out a bearing
Cleaning knocks grease out of bearings. Heat thins it. Time breaks it down. Without a plan to replace what gets lost, your bearing runs dry. This is one of the most preventable causes of failure.
Common lubrication mistakes:
- Skipping lube after cleaning
- Using the wrong grease for washdown chemicals
- Over-lubricating and blowing seals
- Forgetting altogether during busy periods
Avoid this by:
- Creating and sticking to a lube schedule
- Choosing the right grease for your environment
- Switching to auto-lube if manual upkeep is difficult.
Bearings that are properly lubricated last longer, perform better, and save money on callouts and replacements.
How to Spot a Food Processing Weak Point
Not all downtime starts with a bang. In many cases, it starts with something that just looks a little off. Here are a few questions to ask during your next maintenance walk:
- Are your bearings certified for food contact?
- Is the grease visible or leaking?
- Is water pooling beneath any housings?
- Are the units easy to access and inspect?
- Do you have spec sheets on file for audits?
- Are the same bearings failing in the same places?
These small checks can highlight big problems before they get worse.
Checklist: Downtime-Proof Your Bearings
Here’s a simple checklist to help you prevent bearing-related downtime:
✅ Use IP-rated seals suited to your cleaning intensity
✅ Choose grease that withstands washdowns and is NSF certified
✅ Fit housings to sloped surfaces with good drainage
✅ Review lubrication schedules weekly
✅ Avoid generic bearings in food contact zones
✅ Don’t reuse stock from non-food lines without checking compliance
✅ Keep technical documentation handy for audits
Stick this in the maintenance office or laminate it for your site engineer. It could save your shift.
Conclusion: Don’t Let Bearings Undermine Your Whole Operation
Food production is relentless. Your bearings need to be just as tough. A small spec error, a forgotten grease top-up, or a lazy install might not seem like a big deal at first. But those small issues are often what lead to hours of costly downtime.
At Godiva Bearings, we help maintenance teams spec, install, and maintain bearings that are up to the task. Our food-safe range includes polymer housings, stainless inserts, auto-lubrication options, and audit-ready documentation.
📥 Download The Complete Guide to Bearings in Food Production
📞 Speak to our team about the right food processing bearings
Let’s keep your production lines running smoothly and your hygiene scores spotless.
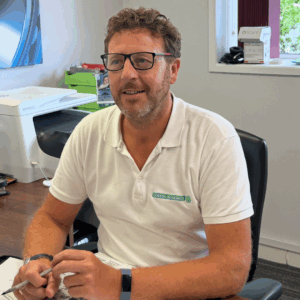
TOM HAMLETT
Tom Hamlett is a respected authority in the global bearings marketplace, with over 35 years of experience in industrial bearings, lubricants, and adhesives across a wide range of industries. As Managing Director of Godiva Bearings, Tom has built a trusted business renowned for its commitment to quality, technical expertise, and ethical service. Under his leadership, Godiva Bearings has remained the UK’s only trade-exclusive bearings supplier, proudly serving engineers and distributors worldwide since 1977. Tom’s in-depth knowledge and dedication have cemented his reputation as one of the most knowledgeable figures in the sector.